A Programmable Logic Controller (PLC) is an industrial computer designed to automate machinery, processes, and entire production systems. The PLC meaning refers to its role as a digital system that receives input signals, processes data, and controls output devices to ensure smooth and efficient operations. Used extensively in industries like manufacturing, oil & gas, and automotive, PLCs are the backbone of modern automation. Understanding the PLC meaning is essential for anyone involved in industrial automation, as these systems help improve efficiency, reduce downtime, and enhance safety in complex processes.
Table of Contents
PLC Meaning: What Is a Programmable Logic Controller (PLC)?
The PLC meaning refers to a Programmable Logic Controller (PLC), which is a specialized tiny computer designed to receive data through its inputs and send operating instructions through its outputs. The fundamental PLC meaning revolves around its role in industrial automation, where it controls a system’s functions using internal logic programmed into it.
Understanding the PLC meaning is essential for industries that rely on automated processes. Businesses worldwide use PLCs to automate critical functions. The PLC meaning extends to its ability to take in inputs from various sources, such as sensors, switches, or buttons, and determine how to respond based on pre-programmed logic. Their outputs control a wide range of equipment, including:
- Motors
- Solenoid valves
- Lights
- Switchgear
- Safety shut-offs
Evolution of PLCs and Their Meaning in Automation
Before PLCs, industrial facilities depended on complex relay-based control systems that were prone to failure. The introduction of PLCs in the 1960s by Richard Morley provided a more reliable and efficient alternative. Manufacturers quickly adopted PLCs, making the PLC meaning synonymous with automation and efficiency in industrial environments.
Today, PLC meaning is deeply embedded in modern industrial control systems. It remains the most commonly used industrial control technology worldwide. Learning the PLC meaning and how these controllers function is an essential skill for engineers, technicians, and automation professionals.
What Does a Programmable Logic Controller (PLC) Do?
A Programmable Logic Controller (PLC) is an industrial digital computer designed to automate electromechanical processes in various industries. Unlike traditional computers, PLCs are built to withstand harsh industrial environments, including extreme temperatures, humidity, dust, and electrical noise. They function as the brain of an automated system, executing predefined logical operations to control machinery and processes efficiently.
Key Functions of a PLC:
They help in emergency shutdowns, fail-safe operations, and hazard detection to protect both workers and equipment.
Automation of Processes:
PLCs execute programmed logic to control mechanical systems in manufacturing, power plants, and other industries.
They replace hardwired relay control systems, offering greater flexibility, scalability, and ease of troubleshooting.
Real-Time Monitoring and Control:
PLCs continuously collect data from sensors and input devices, process it according to the programmed logic, and send signals to output devices.
They ensure precise control of motors, actuators, and other industrial components.
Decision-Making and Troubleshooting:
A PLC can detect errors, system failures, or deviations in operational parameters and initiate corrective actions automatically.
Operators can use Human Machine Interfaces (HMIs) to diagnose issues and reprogram the system if necessary.
Integration with Other Systems:
PLCs communicate with other automation devices, such as Supervisory Control and Data Acquisition (SCADA) systems, Distributed Control Systems (DCS), and Industrial Internet of Things (IIoT) platforms for real-time data exchange and advanced process optimization.
Safety and Reliability:
PLCs are essential in industries requiring high safety standards, such as oil refineries, nuclear power plants, and chemical processing facilities.
What Applications Would You Use PLCs For?
PLCs are widely used across industries to automate and control various systems. Some of the most common applications include:
1. Manufacturing and Production Lines:
- Used to control assembly lines, robotic arms, conveyor belts, and packaging systems in automotive, electronics, and consumer goods industries.
- Ensures high-speed production with minimal errors and downtime.
2. Oil and Gas Industry:
- PLCs monitor drilling operations, manage pipeline systems, and control refineries to ensure safe and efficient processing of crude oil and natural gas.
- Used for leak detection, pressure monitoring, and emergency shutdown systems.
3. Power Generation and Distribution:
- PLCs manage power grids, renewable energy systems (solar, wind, hydro), and substations to optimize energy distribution and maintain system stability.
- Helps in real-time monitoring of voltage, frequency, and load balancing.
4. Water and Wastewater Treatment:
- PLCs automate water purification, desalination, sewage treatment, and pumping stations to ensure clean water supply and efficient waste management.
- Used for controlling chemical dosing, filtration, and UV disinfection systems.
5. Automotive Industry:
- PLCs control automated vehicle assembly lines, welding robots, paint booths, and engine testing systems to improve efficiency and product consistency.
- Used in quality control and defect detection during manufacturing.
6. Food and Beverage Industry:
- Ensures precise mixing, filling, packaging, and temperature control in food processing plants.
- PLCs help maintain compliance with safety regulations by monitoring hygiene and contamination risks.
7. HVAC and Building Automation:
- PLCs regulate heating, ventilation, air conditioning (HVAC), lighting, and security systems in large buildings, hospitals, and data centers.
- They improve energy efficiency and provide remote monitoring capabilities.
8. Pharmaceutical and Chemical Industries:
- Used to control reactors, batch processing, and packaging lines to ensure precise chemical formulations.
- Helps in maintaining compliance with FDA and GMP regulations.
9. Aerospace and Defense:
- PLCs automate testing, control flight simulators, and manage fuel systems in aircraft manufacturing and defense applications.
- Ensures precision in missile guidance systems and other military-grade operations.
10. Mining and Material Handling:
- PLCs control conveyor belts, crushers, drilling machines, and transport systems in mining operations.
- Monitors environmental conditions such as gas levels and ventilation to enhance worker safety.
Why Are PLCs Preferred Over Other Control Systems?
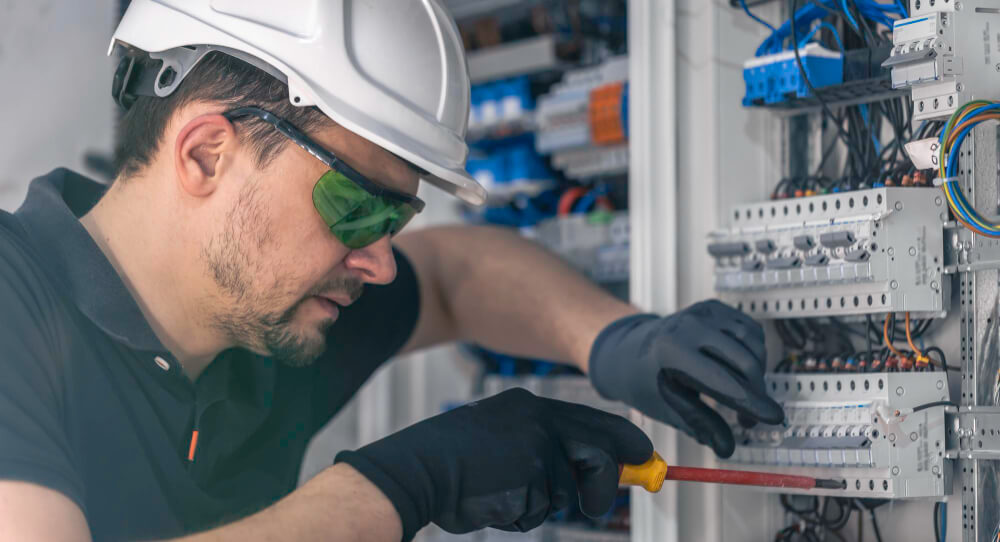
PLCs are preferred over traditional relay-based control systems and even some modern computers due to the following advantages:
- Rugged and Reliable: Designed to function in harsh industrial environments with resistance to dust, moisture, and electrical noise.
- Real-Time Processing: Ensures immediate response to system inputs, which is crucial for safety and efficiency.
- Easily Programmable: Can be modified without extensive rewiring, making them cost-effective and flexible.
- Scalability: Can be integrated with advanced automation technologies like SCADA, DCS, and IoT for enhanced control.
- High-Speed Operation: Suitable for applications requiring millisecond-level response times.
PLCs play a critical role in modern industrial automation, providing businesses with enhanced productivity, operational efficiency, and reduced downtime.
Components of a Programmable Logic Controller (PLC)
A Programmable Logic Controller (PLC) is a specialized computer designed to automate industrial processes, machinery, and entire production lines. PLCs are widely used in industries such as manufacturing, automotive, oil & gas, food & beverage, pharmaceuticals, and transportation.
For a PLC to function effectively, it relies on several key components that work together to process inputs, execute programmed instructions, and generate appropriate outputs. Below are the four main components of a PLC system and their roles in industrial automation.
1. Power Supply
The power supply module is the backbone of the PLC system, as it provides the necessary electrical energy to operate the processor, memory, and I/O modules.
Functions of the Power Supply:
- Converts AC (Alternating Current) voltage (e.g., 120V or 240V) into low-voltage DC (Direct Current) power (typically 24V DC).
- Regulates the voltage to ensure stable and continuous operation of the PLC system.
- Prevents fluctuations in voltage that could disrupt PLC operations or damage sensitive components.
Types of Power Supply:
- Linear Power Supply: Provides stable DC voltage with low noise, commonly used in sensitive applications.
- Switching Power Supply: More energy-efficient and compact, often used in modern PLCs for industrial automation.
Industrial Application Example:
In an automated assembly line, the PLC power supply ensures that all control components, including sensors and actuators, receive the correct voltage to function efficiently.
2. Central Processing Unit (CPU) – The “Brain” of the PLC
The CPU (Processor Module) is the core of the PLC system, responsible for executing logic operations and controlling industrial processes based on pre-programmed instructions.
Functions of the CPU:
- Receives input signals from sensors and devices.
- Processes these inputs according to the programmed logic.
- Sends control signals to output devices such as motors, relays, and actuators.
- Performs mathematical calculations and logical decision-making.
- Monitors the status of connected devices and logs system errors.
Key Components Inside the CPU Module:
- Microprocessor – Executes control instructions and handles communication between different PLC modules.
- Memory (RAM, ROM, EEPROM) – Stores the PLC program, system settings, and real-time data.
- RAM (Random Access Memory): Temporary memory used for execution.
- ROM (Read-Only Memory): Stores the PLC’s firmware and permanent data.
- EEPROM (Electrically Erasable Programmable Read-Only Memory): Retains user programs even when power is lost.
- Watchdog Timer – A safety feature that resets the system if the PLC fails to execute operations correctly.
Industrial Application Example:
In a robotic packaging system, the CPU processes signals from weight sensors, conveyor belt motion detectors, and robotic arms to ensure precise packaging of products.
3. Communication Card – Enabling Connectivity
The communication module acts as the interface between the PLC and external devices, allowing it to communicate with other PLCs, industrial networks, and monitoring systems.
Functions of the Communication Module:
- Facilitates data exchange between the PLC and SCADA (Supervisory Control and Data Acquisition) systems.
- Allows PLCs to connect to industrial networks such as Ethernet/IP, Modbus, Profibus, and Profinet.
- Supports integration with human-machine interfaces (HMIs) for operator control and monitoring.
- Enables remote access to the PLC for troubleshooting, diagnostics, and software updates.
Common Communication Protocols:
- Ethernet/IP: Used for real-time industrial communication over Ethernet networks.
- Modbus (RTU/TCP): A widely used open protocol for PLC-to-PLC and PLC-to-SCADA communication.
- Profibus & Profinet: Industrial communication protocols used in factory automation.
Industrial Application Example:
In an oil refinery, communication cards allow the PLC to exchange real-time data with SCADA systems, ensuring proper control of pumps, valves, and safety systems.
4. Input/Output (I/O) Modules – Interfacing with the Real World
The I/O modules serve as the connection between the PLC and external devices such as sensors, actuators, and control systems.
Types of I/O Modules:
- Digital I/O Modules
- Handle binary (ON/OFF) signals.
- Examples: Push buttons, limit switches, proximity sensors, relays, and solenoid valves.
- Analog I/O Modules
- Handle continuous signals (e.g., voltage or current).
- Examples: Temperature sensors, pressure sensors, and flow meters.
Function of Input Modules:
- Receive signals from external sensors and convert them into data the PLC can process.
- Examples of input devices:
- Temperature Sensors – Detect heat levels in an industrial furnace.
- Pressure Transmitters – Monitor hydraulic pressure in manufacturing processes.
- Photoelectric Sensors – Detect the presence of objects on a conveyor belt.
Function of Output Modules:
- Send control signals to external devices such as motors, alarms, and actuators.
- Examples of output devices:
- Motors & Servo Drives – Control conveyor belt speed in production lines.
- Solenoids & Relays – Open and close valves in fluid control systems.
- Signal Lamps & Buzzers – Provide status alerts in industrial environments.
Industrial Application Example:
In a food processing plant, input modules collect data from temperature sensors, while output modules control cooling systems to maintain the correct food storage conditions.
Summary Table – PLC Components and Their Functions
PLC Component | Function | Example Application |
---|---|---|
Power Supply | Converts AC to DC, provides stable voltage | Ensures continuous operation of control systems |
CPU (Processor Module) | Executes logic, processes inputs/outputs, stores programs | Controls robotic assembly lines |
Communication Module | Enables data exchange between PLCs, SCADA, and HMIs | PLC-to-PLC communication in oil refineries |
Input Modules | Receive signals from sensors and external devices | Detect temperature, pressure, and object presence |
Output Modules | Send control commands to actuators, motors, and alarms | Operate conveyor belts, valves, and pumps |
Conclusion
Understanding the components of a PLC is essential for designing, maintaining, and troubleshooting industrial automation systems. Each component—power supply, CPU, communication module, and I/O modules—plays a crucial role in ensuring that PLCs efficiently control industrial processes.
As automation continues to advance, PLCs will remain a key technology in optimizing efficiency, reducing costs, and enhancing safety across industries.