A power supply is a crucial component in any Programmable Logic Controller (PLC) system. Without a reliable power source, a PLC cannot function properly, making the power supply unit (PSU) an essential part of industrial automation.
A PLC without a power supply is like a car without fuel or a smartphone without a battery. The efficiency and reliability of a PLC system heavily depend on the quality and capability of the power supply unit. Understanding how PLC power supply units work and their different configurations is essential for engineers, technicians, and automation professionals.
In this guide, we will explore how a power supply unit functions in a PLC system, the different types available, and factors to consider when selecting a power source for your automation needs.
Table of Contents
What Is a PLC Power Supply?
The power supply in a PLC system converts high-voltage alternating current (AC), commonly 120V or 240V AC, into a stable, lower-voltage direct current (DC), typically 24V DC, that the PLC and its components require to operate.
Functions of a PLC Power Supply:
- Voltage Conversion: Steps down high AC voltage to a usable DC voltage.
- Voltage Regulation: Maintains a stable output voltage for reliable operation.
- Power Distribution: Supplies energy to the CPU, input/output modules, and other PLC components.
- Protection Mechanisms: Includes fuses, circuit breakers, and surge protection to prevent damage.
- Backup Power Storage: Some PLCs include battery backups to retain memory during power failures.
How It Works
- Line Voltage Input: The power supply unit receives 120V or 240V AC from the main power grid.
- Voltage Transformation: A transformer steps down the voltage to a safer level.
- Rectification: The power supply converts AC into DC voltage using rectifier circuits.
- Filtering & Regulation: Capacitors and regulators smooth and stabilize the power source.
- Output Distribution: The power supply unit distributes DC power to the PLC and its components.
Without an efficient power source, a PLC system would experience failures, incorrect operation, or even permanent damage.
Types of PLC Power Supply Units
1. Built-in Power Supply Units
Many compact PLCs come with an integrated power supply unit. These are designed for small automation tasks and provide a simple power source without needing additional components.
Features:
- Directly connects to 120V or 240V AC.
- Converts and supplies 24V DC for PLC operation.
- Often includes low-power outputs for sensors and actuators.
Pros: ✅ Saves space in control cabinets ✅ Reduces installation time ✅ Simplifies wiring
Cons: ❌ Limited power output ❌ Not suitable for large-scale applications
2. Modular Power Supply Units
Larger PLC systems typically use modular power supply units, which are separate from the CPU. These are mounted in the PLC rack or backplane and provide higher current ratings.
Features:
- Separate power supply unit with dedicated power distribution.
- Can handle higher currents (2A to 50A).
- Provides power to multiple PLC modules.
Pros: ✅ Scalable and flexible ✅ Suitable for complex automation systems ✅ Supports high-power components
Cons: ❌ Requires additional wiring and setup ❌ Takes up more cabinet space
3. External DIN-Rail Mounted Power Supplies
For applications requiring more power source flexibility, external power supply units are mounted on a DIN rail inside the control cabinet.
Features:
- Can provide 24V DC, 12V DC, or other required voltages.
- Supports both PLC and external field devices.
- Available in multiple power ratings.
Pros: ✅ Ideal for high-power automation systems ✅ Can power multiple devices ✅ Reduces stress on internal PLC power circuits
Cons: ❌ Requires careful selection to match system requirements ❌ Needs additional wiring and protection circuits
Choosing the Right PLC Power Supply
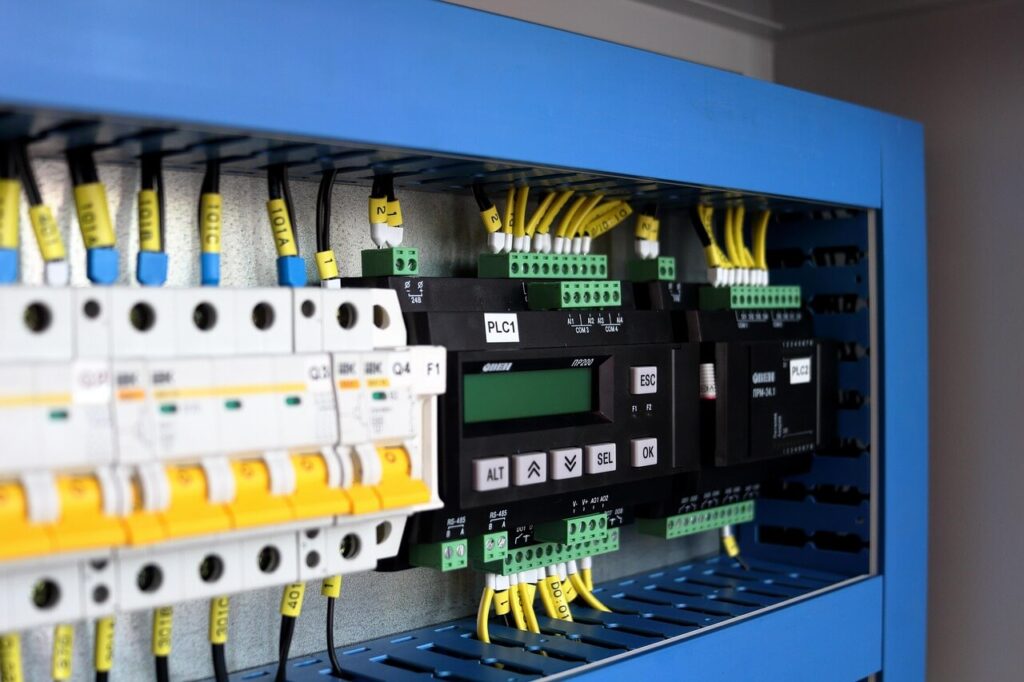
Selecting the right power supply unit depends on several key factors:
- Input Voltage Compatibility:
- Common AC inputs: 120V, 240V
- Common DC inputs: 12V, 24V, 48V
- Current Rating (Amps):
- Small PLCs: 2A to 10A
- Large systems: 10A to 50A
- Must match the total current demand of all PLC modules and field devices.
- Backup Power Needs:
- Some PLCs include battery backup or uninterruptible power supply (UPS) for memory retention.
- Protection Features:
- Surge protection, circuit breakers, and temperature regulation improve system reliability.
- Scalability:
- Modular power supply units allow for future expansion without major redesigns.
Field I/O Power Supply Considerations
A common misconception is that the power supply unit of a PLC also powers the inputs and outputs (I/O) directly. However, in most cases:
- The PLC power supply unit powers only the CPU and communication modules.
- Sensors, actuators, and other field devices require separate power sources.
- Field devices may use 24V DC, 48V DC, or even 120V AC, depending on the application.
To ensure proper operation, always verify the power supply specifications for both PLC and field devices.
FAQs About PLC Power Supply Units
What is the function of a PLC power supply unit?
A PLC power supply unit converts high-voltage AC power (e.g., 120V or 240V) into low-voltage DC power (typically 24V DC) to operate the PLC system and its components.
What are the different types of PLC power supply units?
There are three main types:
Built-in power supply units (integrated within small PLCs)
Modular power supply units (separate from the CPU, used in large PLC systems)
External DIN-rail mounted power supplies (used for additional power flexibility)
Can a PLC power supply unit power input and output (I/O) devices?
No, the PLC power supply unit typically only powers the CPU and communication modules. Field I/O devices, such as sensors and actuators, require a separate power source.
How do I choose the right PLC power supply?
Consider these factors:
Input voltage compatibility (120V AC, 240V AC, or 24V DC)
Current rating (ensuring enough power for all PLC components)
Backup power needs (for memory retention)
Protection features (e.g., surge protection, fuses)
Scalability (modular power supplies allow for future expansion)
What happens if I use the wrong voltage for my PLC power supply?
Using the wrong voltage can damage the PLC, cause operational failures, or even lead to electrical hazards. Always check the manufacturer’s specifications before installation.
Why do some PLCs require an external power supply?
Larger automation systems often need more power than built-in PLC supplies can provide. An external DIN-rail power supply ensures stable power distribution to both the PLC and connected field devices.
Conclusion
A PLC power supply unit is a critical component that determines the stability and performance of an automation system. Whether you use a built-in power supply, a modular power source, or an external DIN-rail power supply, selecting the right unit is essential for seamless operations.
By understanding the different power supply options, voltage requirements, and power distribution methods, engineers can design reliable PLC systems that minimize downtime and maximize efficiency.
Looking for more PLC insights? Stay tuned for our next article on PLC CPUs and processing units!